A pellet maker, commonly referred to as a pellet mill or pellet press, is a type of machine designed to convert raw materials into small, cylindrical pellets. mill pellet machine can be made from a variety of materials, including wood, biomass, animal feeds, and other organic materials.
The process not only facilitates the recycling of waste materials but also aids in the efficient storage, handling, and use of different substances. Let's delve into the specifics of pellet makers, including their operation, types, applications, and tips for maintenance.
How a Pellet Maker Works
The operation of a pellet maker involves several key steps, which can vary slightly depending on the type of machine and the material being processed:
Feeding the Material: Raw materials are fed into the pellet maker's hopper. For optimal pellet quality, the material often requires pre-processing to achieve the correct size and moisture content.
Compression: Inside the pellet maker, the material is compressed through a die by rollers. The die is a metal piece with holes through which the material is forced, taking on the shape of small, dense pellets. The pressure and friction generated in the process heat the material, helping to bind it together.
Formation of Pellets: As the material passes through the die, it forms long, cylindrical strands. These are then cut into pellets by a sharp blade or knife mechanism to the desired length.
Cooling: The freshly made pellets are hot and soft. They are cooled, typically in a cooling conveyor or bin, to harden and stabilize before storage or use.
Types of Pellet Makers
There are two primary types of pellet makers, each suited to different production needs:
Flat Die Pellet Makers: These machines use a flat die with holes and rollers that press the material through the holes. Flat die pellet makers are simpler, more compact, and typically used for smaller-scale production or by individuals for home use.
Ring Die Pellet Makers: These are more complex machines designed for large-scale production. The die in these pellet makers is a large ring with holes on the inside. Rollers press the material through these holes as the ring spins. Ring die pellet makers are more efficient for continuous, high-volume pellet production.
Applications of Pellet Makers
Pellet makers are versatile machines with a wide range of applications across various industries:
Biomass Pellets: Creating pellets from wood, sawdust, crop waste, and other biomass materials for use as biofuel or in bioenergy generation.
Animal Feed: Producing feed pellets from grains, forage, and supplements for livestock, poultry, and aquaculture.
Waste Management: Converting agricultural, industrial, and municipal waste into pellets for easier handling, disposal, or as a source of energy.
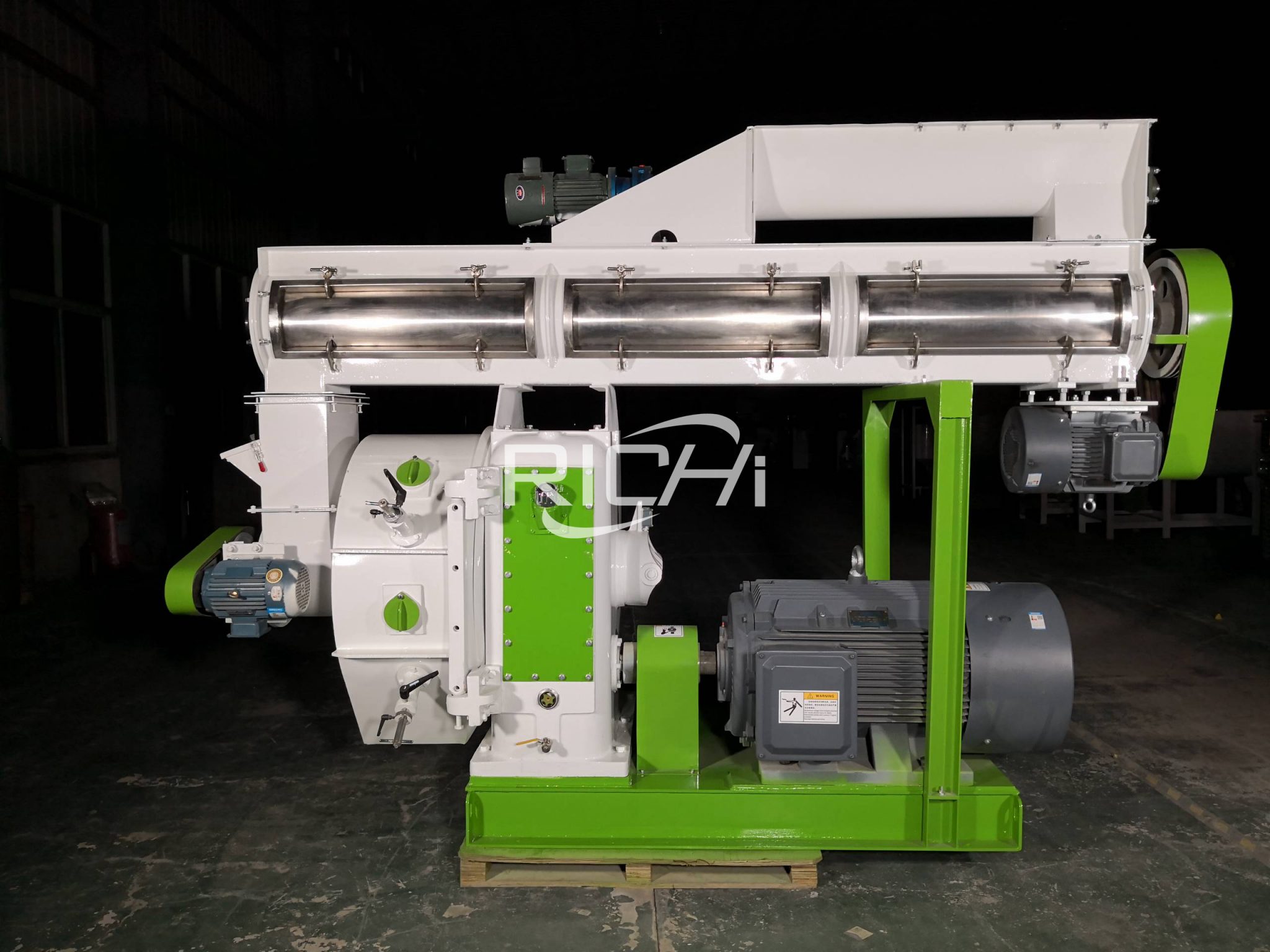
machine a pellet for Pellet Makers
Proper maintenance is crucial for ensuring the longevity and efficiency of a pellet maker:
Regular Cleaning: Keep the machine clean, especially the die and rollers, to prevent blockages and ensure consistent pellet quality.
Lubrication: Regularly lubricate moving parts to reduce wear and tear.
Inspection and Replacement: Frequently inspect the die and rollers for wear. Replace these parts as needed to maintain the quality of the pellets and the efficiency of the machine.
Conclusion
Pellet makers are essential tools in modern manufacturing and recycling processes, transforming a wide range of materials into compact, uniform pellets. Whether for fuel, feed, or waste reduction, understanding the operation and maintenance of these machines can help users maximize their benefits. With the right care and operation, a pellet maker can significantly contribute to more sustainable and efficient production and energy use practices.